2024 is coming to an end, but the electric transformation at SEAT S.A. keeps going full throttle. Reflecting on the year we’re leaving behind, we’ve faced many changes on our journey towards the electric future. “2024 has been the year of consolidation of our transformation, moving towards smart and connected production, with more agile and optimised processes, to manufacture electric urban cars and turn SEAT S.A. into an electric mobility hub in Europe”, explains Markus Haupt, Vice-President for Production and Logistics. So, let’s scroll through the company’s electrification journey as we get ready for an electrifying 2025.
Battery system assembly plant. With an investment of 300 million euros and 64,000 m2, the construction of the future Workshop 20 has made unstoppable progress in just one year. The plant will have the capacity to manufacture 1,200 batteries daily, one every 40 seconds, for assembly in the Volkswagen Group’s electric urban cars produced in Martorell, in order to optimise logistical processes and reduce the carbon footprint.
PXL press. Electrification has also brought about the modernisation of the press facilities, with the major addition of the new PXL press, already up and running. This 6-press system is more powerful and efficient with 81,000 kN of force and a production rate of up to 4 million parts per year, equipping the latest connected technology. It will be used to manufacture the body parts for the CUPRA Raval and other urban electric vehicles for the Group.
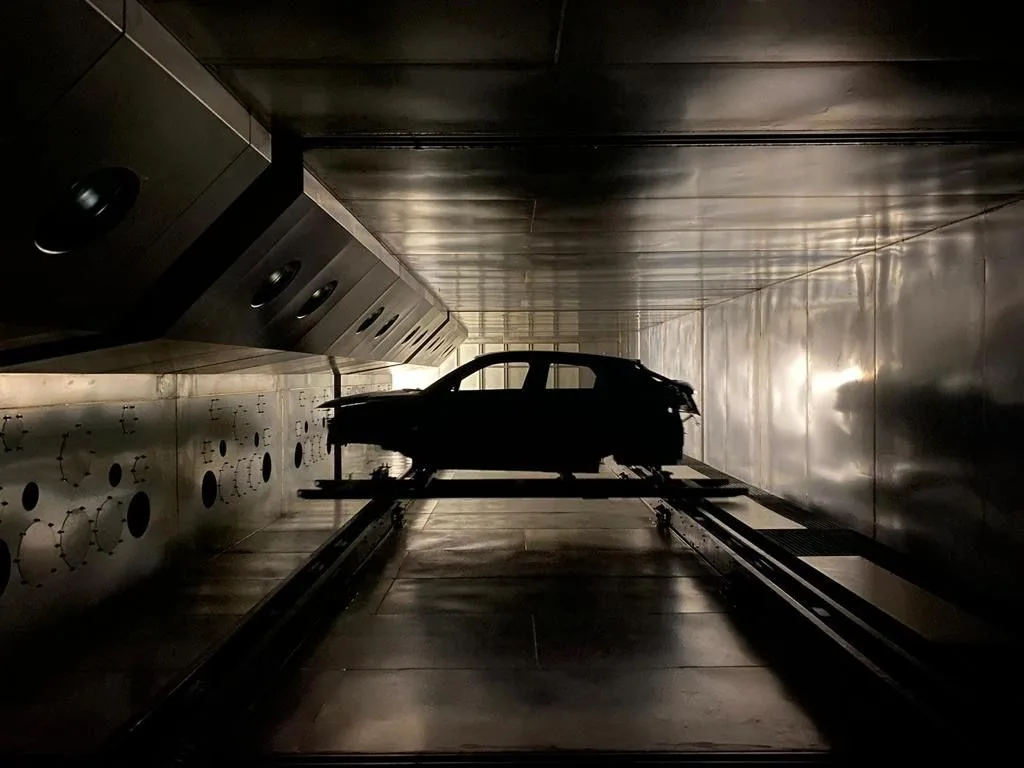
KTL oven. The new KTL oven in Martorell is the Volkswagen Group’s first all-electric transversal paint-drying oven. Based on the most advanced technology, this optimised tool is 42% shorter than a conventional oven, minimising heat loss and saving 2,500 tonnes of CO2 emissions per year.
Assembly line transformation. This year, the production of the SEAT Ibiza and SEAT Arona has also been relocated to line 3, in order to prepare and adapt production line 1 for the arrival of the electric urban car, along with the first pre-series cars.
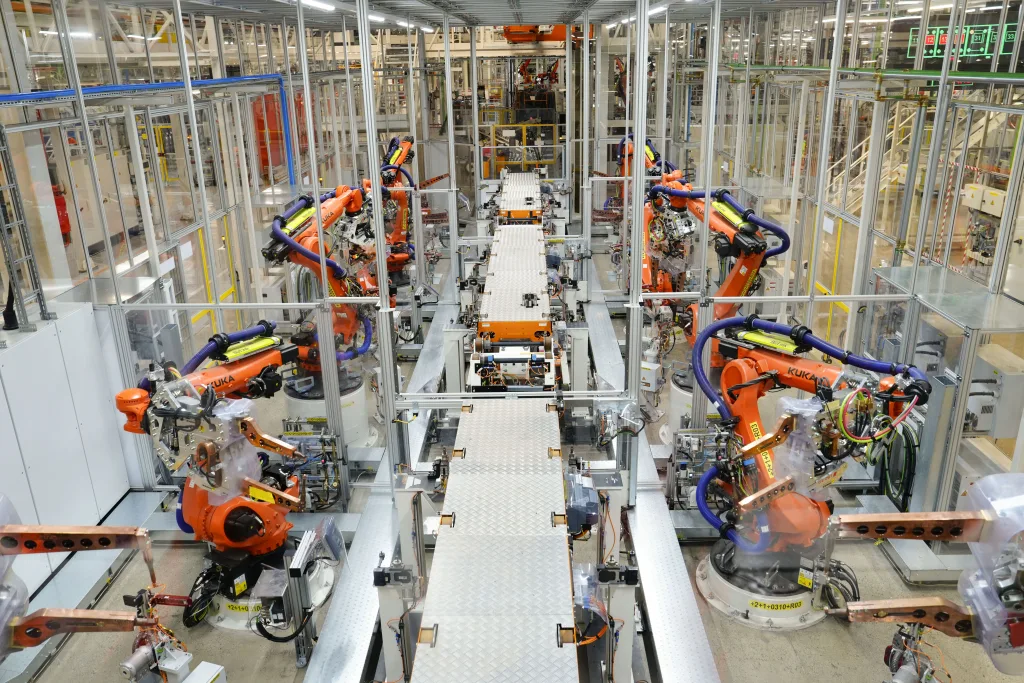
P-Bootcamp electronic hub. This initiative aims to ensure the fine-tuning of the electric urban car electronics by using tools such as the P-Golden Car, a prototype that simulates the behaviour of the software and allows the entire programming of the vehicle to be configured and analysed before it reaches the assembly line.
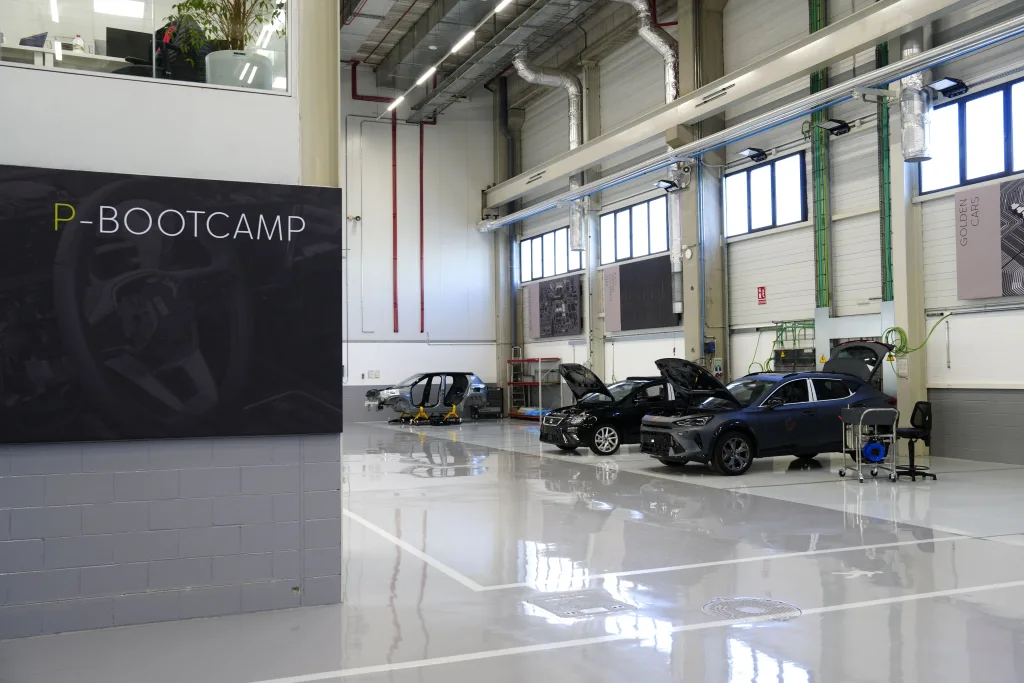
More than 170,000 hours of training. Preparing the company’s employees for the transition to electrification has continued to play a key role in 2024, with more than 170,000 hours of training at all levels to guarantee the ongoing and demanding adaptation of the teams to achieve success in the production of the electric urban car.