Audi builds the electric motors for the Premium Platform Electric (PPE) at the world’s largest powertrain plant in Győr, Hungary. The drive systems will initially be used in the Audi Q6 e-tron series, which is produced in Ingolstadt. Győr manufactures the PPE drive systems on an area of around 15,000 square meters (approx. 160,000 sq ft), in addition to producing stator and transmission components and assembling the axles. Csaba Imre Benke, Head of the Electric Drive Systems Product Segment in Győr and responsible for the production of the PPE drive systems, explains how Audi is setting new standards with the production of electric drive systems for the PPE.
Can you give us an idea of the scope involved in producing the PPE drive systems?
Csaba Imre Benke: To produce the electric motors for the PPE, the brand with the four rings has installed three new production lines. The production line for stators has 28 work steps, the one for transmission components has 15. Assembling one axle requires more than 190 individual steps.
How many employees are involved and how many electric motors do you produce?
Csaba Imre Benke: All told, around 700 employees are involved in producing the PPE drive systems. In Győr, three shifts are able to mass-produce 2,000 electric motors for the PPE every day. The electric drive systems we produce here are for the PPE models from Audi and Porsche.
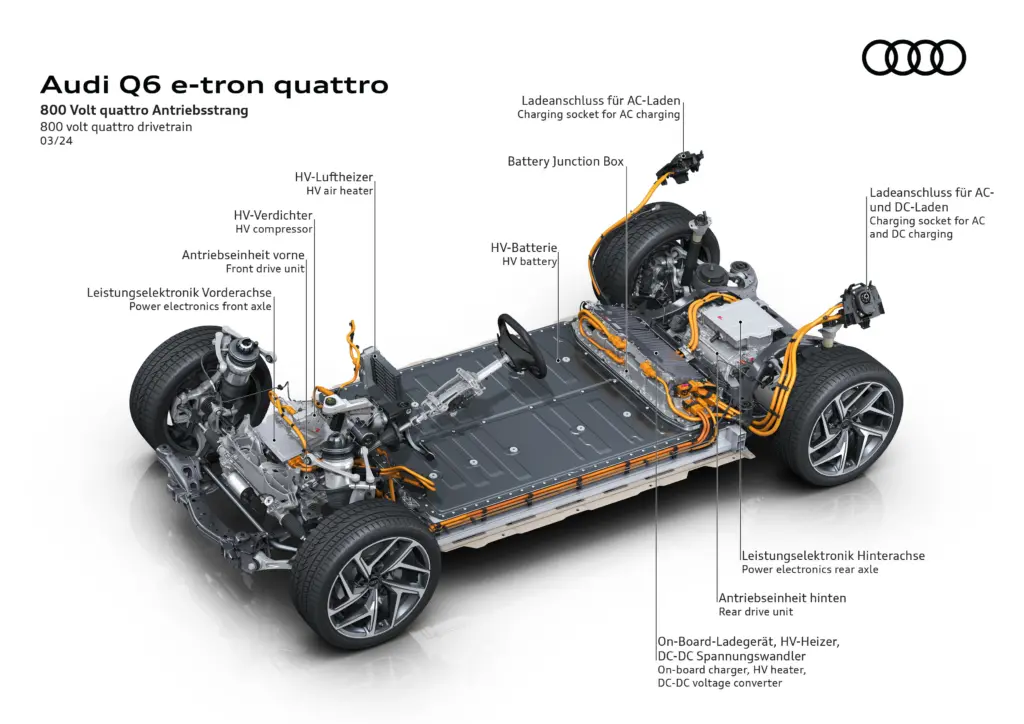
What previous experience does the Győr plant have in producing electric motors?
Csaba Imre Benke: Producing for the PPE naturally meant we had to learn a number of work steps at the new production stations. It took our employees around 20 days of training each to learn everything. But we are not starting from scratch! We have made more than 500,000 electric motors since 2018. It goes without saying, our experience benefits us. Especially since we will be gradually increasing our vertical range of manufacture for electric motors. Right now, we are manufacturing the stators and transmissions ourselves and also assembling the axles here in Győr.
What are the main differences between producing the drive systems for the PPE and the electric motors you used to make?
Csaba Imre Benke: As far as production goes, the powertrain for the PPE is in a whole different league. Due to the technical differences, the lines look completely different. For the PPE alone we use 15 automatic bending machines to make the three-dimensional hairpin windings and two systems to laser-weld the ends after that. Each stator contains 140 meters of copper wire. It takes a total of 235 laser welds to make one. Compared to combustion-engine models, electric drive systems generally have fewer bolted fastenings but require more pressing, so more robots can be used. In addition to increasing automation rates, our overarching aim is to further increase our vertical range of manufacture for future electric motor projects. For example, we still had to purchase the transmission for the Audi e-tron. On the PPE, we manufacture it ourselves.
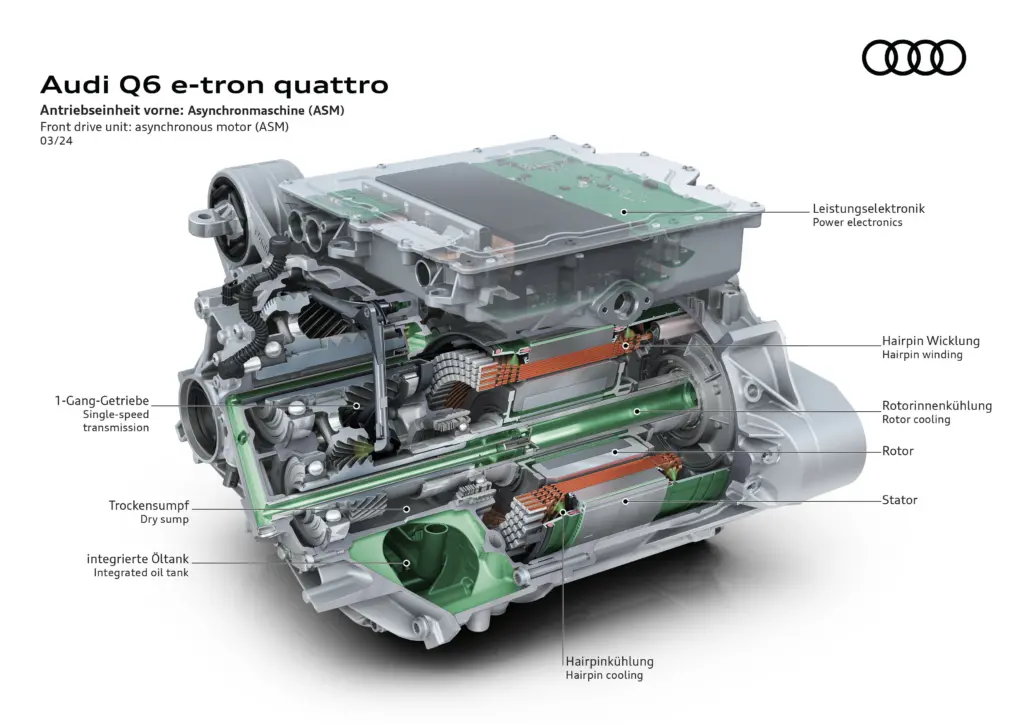
People are driving the electrification of the site. How long does it take to qualify employees for the PPE and what qualification levels are there?
Csaba Imre Benke: The first level is a relatively simple basic training that takes about two hours for employees working near the production line. These tasks are not much different from building combustion models. The difference is our “High-voltage sensitization” course that every employee has to take. Courses for more complex tasks take a whole workday. Our “electrical specialists” undergo training for several days. “Electrical specialist in charge” is the highest level. It can take about three months to train to that level depending on the employee’s level of basic training. For the most part, we are relying on existing personnel from our combustion world. Around 2,000 employees have been trained for electrification in Győr since 2022.
Interesting facts about the PPE drive system
The essential components of the Premium Platform Electric (PPE) are the high-voltage battery and the electric drive systems. The electric drive systems+ for the PPE are built in Audi’s powertrain plant in Győr, Hungary. The fundamental development goal was a scalable electric drive system with high integration, efficiency, and power density.
The newly designed drive system consists of the three main components electric motor, power electronics (pulse width modulating inverter), and transmission. Overall, each of the components stands out due to greater efficiency. They are designed to be scalable and more compact.
As a result, torque can be varied by adjusting the length of the electric motor. Torque at the wheel and the maximum speed are influenced in the transmission by the pairing of the gears. The new electric motors also require about 30 percent less installation space than the engines previously used in Audi’s electrically powered models. Additionally, the new design has made it possible to reduce the weight by about 20 percent.
Increased efficiency
A significant advantage of the redeveloped electric motors is their efficiency. The primary contributors to this are a new hairpin winding in the stator, silicon carbide semiconductors in the pulse width modulating inverter, and an electric oil pump in the transmission. The new hairpin winding maximizes the current conduction in the electric motor’s stator. This method also allows for higher winding counts: The fill factor is now 60 instead of 45 percent compared to the previously used conventional windings. Thanks to rotor oil cooling, Audi was also able to avoid using rare earths to the greatest possible extent. In total, losses caused by drag in the electric drive systems fell significantly by about 50 percent.
Increased power density
The direct cooling of the electric motors with oil, which was used for the first time, keeps components like stator winding and permanent magnets in the rotor in the optimal temperature range. As a result, the drive system’s power-to-weight ratio for the PPE electric drive system is about 60 percent higher than that of the first-generation electric drive systems.
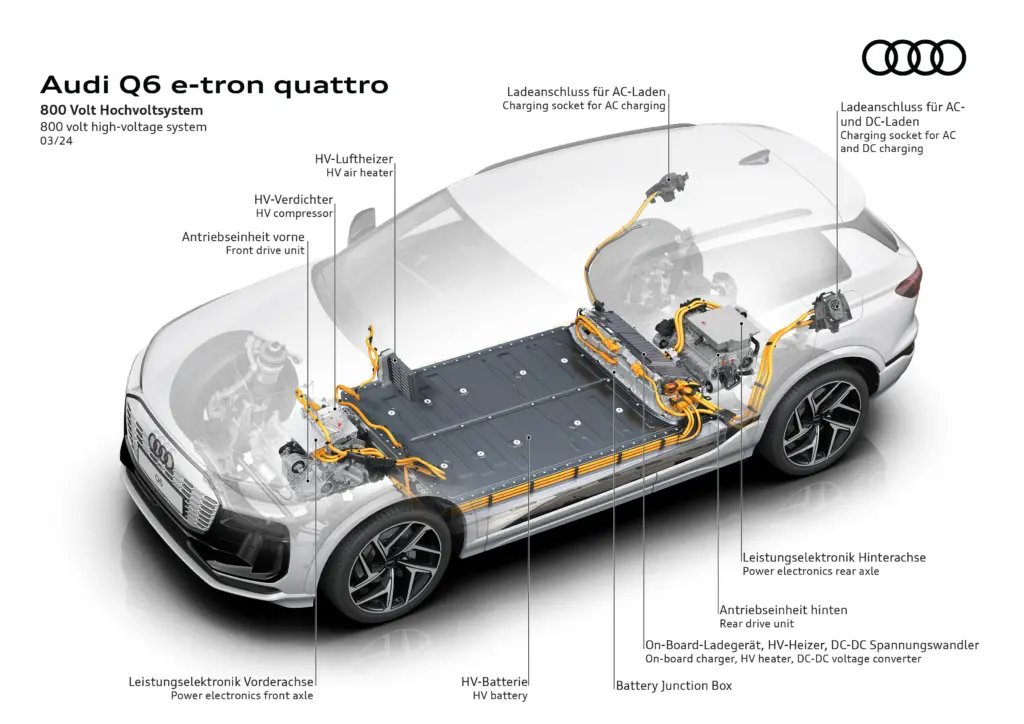
Optimized acoustics
The redeveloped electric drive systems for the PPE also stand out due to particularly quiet and comfortable acoustics. Motor mounts molded on the structurally optimized housing, improved tooth geometry, and a segmented rotor contribute to this.
Expanded vertical integration
Another important factor for the successful development of the PPE electric drive systems is the significantly expanded vertical range of manufacture in Győr. The largest powertrain plant in the world not only manufactures electric motors, but also a majority of the transmissions.
Tailor-made electric motors
When accelerating under full power, an asynchronous motor (ASM) on the front axle goes into action. The ASM does not contain any magnets; it generates its magnetic field through induction and can therefore, if necessary, spin freely without significant drag losses. On the rear axle there are extremely compact permanent-magnet synchronous motors (PSM), which are exclusive to the Q6 e-tron series.
800-volt architecture saves installation space and weight
The 800-volt technology used in the PPE offers more than just high performance and short charging times. As a result of the higher electric voltage, thinner cables can be used to wire the battery and the electric motor. This reduces installation space, weight, and consumption of raw materials. Another advantage of the 800-volt technology is lower heat loss, which reduces the cooling required.