- Bentley’s 3D printing, or industry-termed Additive Manufacturing (AM), is carried out inside the company’s Engineering Technical Centre at its headquarters in Crewe
- Significant investment into AM facilities has increased capability to print prototype parts for the development of Bentley’s first fully-electric car, the world’s first Luxury Urban SUV, to be revealed in 2026
- Bentley’s AM team has produced more than 125,000 3D printed parts over 25 years of operations in Crewe
- Original facility was located in the oldest building at the Pyms Lane site, which is being transformed into the future BEV assembly line
Bentley Motors is marking 25 years of Additive Manufacturing (AM) – widely known as 3D printing – at its headquarters in Crewe, having invested significantly into its facility and technologies in recent years. The journey, which began with a commitment to in-house 3D printing to support the development of Bentley’s first generation Continental GT, has evolved into a state-of-the-art facility that’s home to 13 machines operating six cutting-edge technologies.
Originally housed in the oldest building at the Pyms Lane site, A1 – which is now being transformed into the future assembly line for Bentley’s first BEV – the 3D printing facility has been relocated into the company’s new Engineering Technical Centre, reinforcing Bentley’s position at the forefront of innovation in advanced product development and manufacturing techniques.
Bentley’s Additive Manufacturing facility leverages a diverse range of advanced technologies, each offering unique printing capabilities that support the entire development and production lifecycle across multiple business areas.
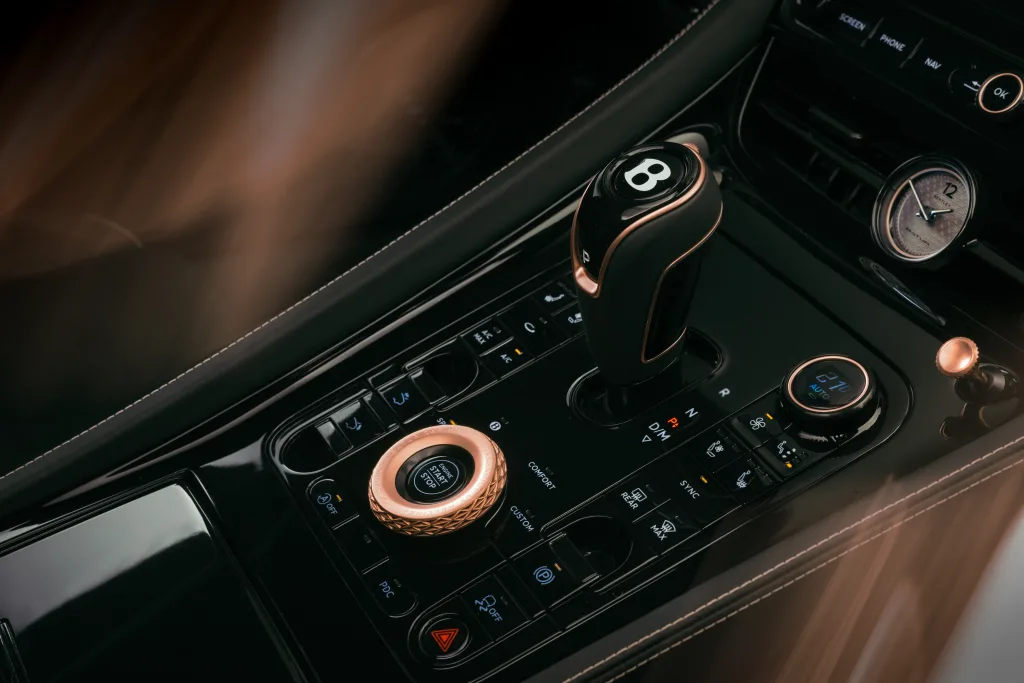
A recent industry first example was on ‘The Black Rose’, a special customer commission, and one of only three right-hand-drive Baturs. The first ever expression of three dimensional printed solid rose gold was used, adding up to 210 grams of hallmarked 18-karat rose gold to the interior of the coachbuilt coupe at key driver touchpoints.
Commenting on the milestone, Dr. Matthias Rabe, Bentley’s Member of the Board for R&D, said:
“Additive manufacturing continues to play a vital role in the product development process, and our capability and expertise in this field has gone from strength to strength. The ability to rapidly produce and iterate components has advanced how we develop our models and offers further opportunities as we electrify our model range and create our next generation of extraordinary cars.”
The AM facility enables optimal material and process selection for every application. From large, functional components produced through Fused Deposition Modelling (FDM) to aerodynamic test models created by Multi-Jet Fusion (MJF) technologies.

The team has even 3D printed a W12 engine block scaled down to just 5 mm wide that still retains every detail of the engine thanks to a Lithography-based Metal Manufacturing (LMM) technology – a pioneering approach to 3D metal printing that delivers industry-leading precision. These technologies support everything from scale models and rapid prototyping, to ‘single-print’ parts and bespoke tooling solutions that not only accelerate the product development process, but make it more sustainable through reducing waste materials.
Beyond product development, Bentley’s Additive Manufacturing expertise has also made a positive difference in the local community and beyond. The team produced over 20,000 items of PPE to support NHS staff and local care homes during the COVID-19 pandemic, and has been exploring methods to make their activities more sustainable, such as taking excess polymer powder from the MJF process and reusing it as a filament in FDM printing – which accounts for around 60 per cent of the material output from the Additive Manufacturing facility.