- New Audi Vehicle Safety Center launched at the inauguration of the incampus technology park
- Significantly improved and more efficient testing facilities, even for future requirements
- Around 100 million euros of investment in the advancement of passive safety
The new Audi Vehicle Safety Center on the incampus premises in Ingolstadt provides significantly improved and state-of-the-art crash test facilities. Around 100 million euros were invested in the facility. Among its features are a 250-meter (820 ft) run-up track, a mobile 100-ton crash block, and the ability to collide two vehicles at a 90-degree angle. As a premium brand, Audi is committed to meeting heightened requirements that go beyond current international standards.
The new Audi Vehicle Safety Center (AFZ) in Ingolstadt will officially go into operation as part of the inauguration of the incampus technology park. The facility is Audi’s most important development facility in passive safety: Around 100 employees will work here, covering all test scenarios that are known and relevant today. During the design phase, it was ensured that the facility would be capable of performing tests that go well beyond the current requirements of Audi’s many markets. This means that the facility can be flexibly adapted to future developments.
More tests possible in the future
Audi invested a total of around 100 million euros in the facility, with construction taking three years. The new Vehicle Safety Center can handle a greater number and variety of vehicle crash tests than the crash hall previously used on the Ingolstadt plant site. The facility is also much more extensive, with a core area of 130 by 110 meters (430 by 360 ft) and a height of 20 meters (65 ft). The integrated crash arena consists of a support-free area measuring 50 by 50 meters (165 by 165 ft), while the opposing run-up tracks have a total length of 250 meters (820 ft), enabling tests at speeds exceeding today’s usual requirements. An additional lane also allows right-angle car-to-car crashes involving two vehicles.
“Safety is a top priority at Audi. Our new vehicle safety center is impressive proof of this commitment,” says Oliver Hoffmann, Member of the Audi Board of Management for Technical Development. “Today’s Audi models achieve outstanding results in globally valid test procedures. But we’re not resting on our laurels. Instead, we’re continuing to improve our development and testing capabilities.”
A wide range of testing capabilities
A crash block weighing 100 tons is arranged in the crash arena so that it can be moved and rotated, enabling a highly efficient process for the many different types of crash tests. The area is crisscrossed with several crash lanes, enabling research on collisions between two vehicles and integral safety. The so-called “flying floor” also allows vehicles to be driven sideways against obstacles. Each vehicle undergoes a high double-digit number of test scenarios before it is launched.
Belt systems and airbags are being developed even more efficiently thanks to a novel coasting slide with a delay unit. State-of-the-art high-speed cameras and energy-efficient LED lighting systems facilitate the team’s work in the Audi Vehicle Safety Center. A dummy lab, component test stands, workshops, and offices complete the building.
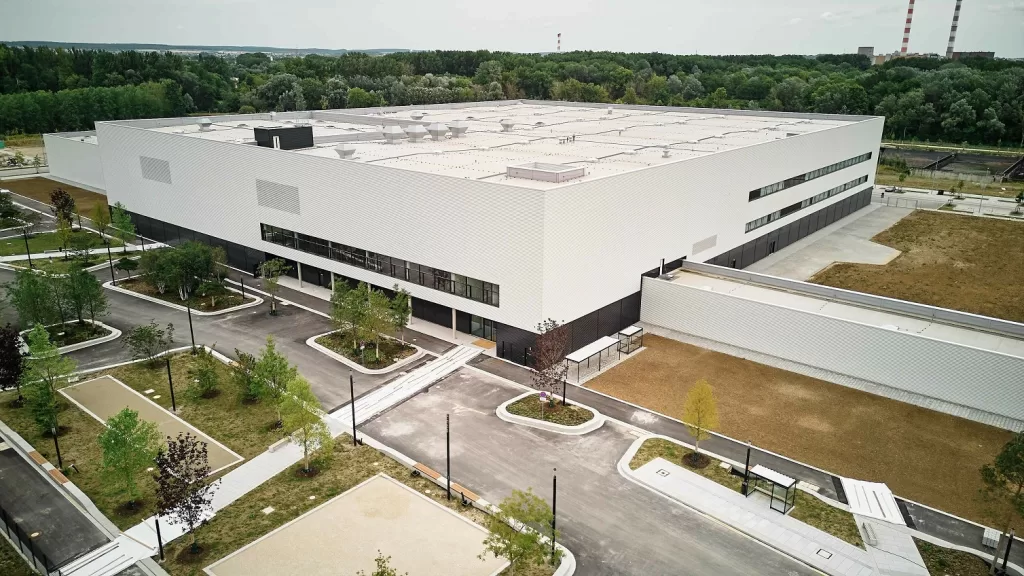
The concept, technology, and adjacent expansion areas were planned to meet the requirements of many years to come. They allow the Audi Vehicle Safety Center to be used flexibly and ensure that it can be equipped to meet new technological requirements, even as standards and regulations in global markets continue to tighten.
Closely coordinated simulations and tests
More than 60 crash test dummies of various types are used in the new crash arena – from an 18-month-old toddler to an adult weighing 102 kg (225 lb). The sophisticated THOR dummies use up to 150 sensors to obtain relevant data during the tests.
High-speed cameras and motion tracking are used to capture the sequence of events during crash tests. A large number of sensors provide physical readings. 3D scans are used to process post-test deformations digitally. All this data is fed into a back-end system. The system also includes data analyzed by experts from other test labs in Europe, Asia, and America.
These days, practically all accidents can be simulated, whether they involve pedestrians or head-on and side-on collisions. Every month, the specialists at Audi perform tens of thousands of crash simulations well before the first prototype is even built. For the crash design of the body of a single current model alone, more than 60,000 calculations are made for up to 100 different load cases. The new Audi IT Center, also located nearby on the incampus site, plays an important role here.
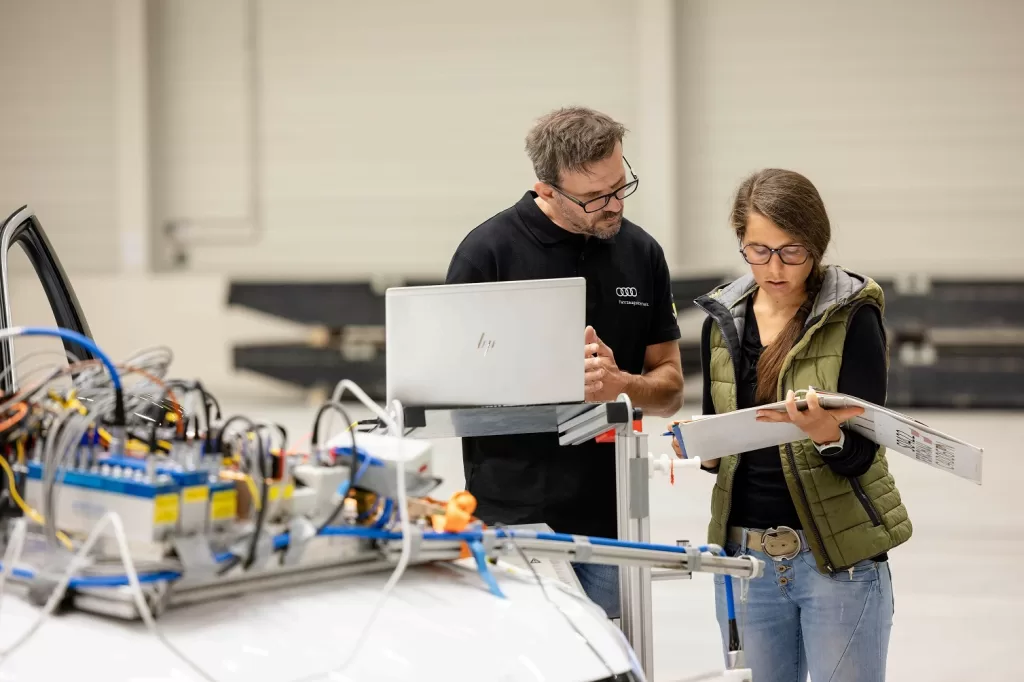
Despite the rapid progress in simulation technology, actual crash and component tests remain essential. This is because the various national authorities in countries where Audi models are marketed have approval procedures that require physical crash tests. In product development, on the other hand, the two methods are highly synergistic, with findings from both simulation and physical testing flowing into the process.
Long tradition of passive safety at Audi
Passive safety, i.e., everything that reduces the consequences of an accident for car occupants and road users, including pedestrians, has a long tradition at Audi. DKW was already working in this field more than 80 years ago when the DKW F7 was put through systematic rollover tests to gain insights into design safety. In fact, those were the first crash tests in automotive history. Later, the specially built facility in Auto Union’s central testing department allowed reproducible collision testing.
Another major step followed in 1970 with the inauguration of the first crash hall in Ingolstadt. After its construction, the building was used for over 50 years, during which time it was repeatedly modified and adapted to meet new requirements.
In 1972, crash test dummies were used for the first time and became increasingly sophisticated and versatile over the years. In 1986, Audi introduced a self-patented innovation: the procon-ten (programmed contraction and tension) safety restraint system. In a head-on collision, the steering wheel retracts, and the front belts tighten by moving the engine toward the passenger compartment via steel cables and pulleys. The system significantly reduced the risk of head injuries for the driver in the event of an accident. It was not until the widespread introduction of airbags that this invention was improved on.
Over the past 25 years, testing has progressively focused on digitalization – starting with the 1999 Audi A3. Ongoing work with ever-larger volumes of data laid the foundations for the increasingly intelligent algorithms used today. What’s more, machine learning has played an ever-greater role in recent years. For example, machine learning has been harnessed to improve the software of the airbag control unit.
In recent years, all the Audi models tested, including the fully electric models, have achieved top ratings in both active and passive safety in tests designed by consumer protection organizations worldwide, such as Euro NCA and China NCAP. Incidentally, electric vehicles are subject to the same stringent requirements as models with conventional drive systems.
Tests in the United States also achieve similar results: So far this year, no fewer than seven Audi models have received an IIHS TOP SAFETY PICK award from the Insurance Institute for Highway Safety – five of them TOP SAFETY PICK+ in the highest category. In addition to crashworthiness, other factors, such as crash avoidance and lighting technology, were also evaluated.
The new Audi Vehicle Safety Center represents the next major step in the advancement of passive safety at Audi. The presence of other institutions involved in safety – including Volkswagen’s software subsidiary CARIAD and the Technische Hochschule Ingolstadt – on the incampus facilitates interdisciplinary exchange.