- Ford has a new state-of-the-art Rolling Road Wind Tunnel (RRWT) which enables improved aerodynamic research and development for next-generation Ford electric, hybrid and internal combustion engine vehicles
- Rolling Road surface in the wind tunnel is capable of reaching 200 mph (322km/h) along with air speed so aerodynamicists can replicate conditions similar to those experienced on the road or track, aiding research while allowing more opportunity for additional development
- The Rolling Road Wind Tunnel was used to help develop the all-new Mustang Dark Horse, which has the most downforce of any 5.0-litre Mustang to date
Wind tunnels have long been used to design and test aerodynamic and energy efficient vehicles. Now, Ford has combined the latest wind tunnel technology with the equivalent of a vehicle-sized treadmill to help create its next-generation of production vehicles, including the first-ever Mustang Dark Horse.
Capable of simulating wind and road surface speeds of 200 mph (322km/h), the Rolling Road Wind Tunnel (RRWT) supports testing for efficient and performance-driven vehicles across the Ford lineup – including the next generation of Ford electric, hybrid and internal combustion engine (ICE) vehicles.
One key benefit of the RRWT is that it gives more accurate data in terms of both wind drag and downforce compared to other earlier wind tunnel designs, which are key factors when optimising for range and efficiency. It also allows for more in-house testing that simulates open-road conditions, which can help reduce design costs while also accelerating the design process.
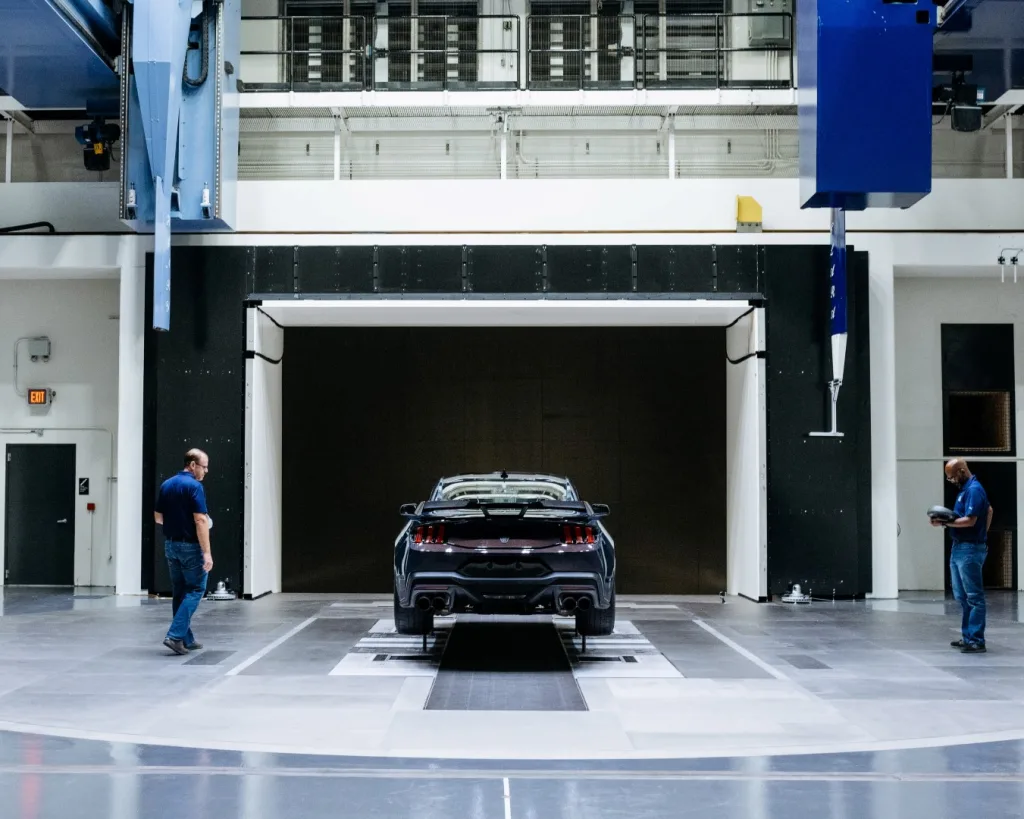
“The closer we can get to reality in the lab, the better and faster we can create more energy efficient vehicles with great on-road and track stability,” said John Toth, Ford’s North America Wind Tunnels Engineering Supervisor. “Testing while the wheels and tyres move is instrumental to improving aerodynamics for track-ready vehicles, like Mustang Dark Horse which has to balance both aerodynamic drags and downforce.”
A new five-belt rolling road system can replicate real-world drag through a rolling road aerodynamic tunnel that enables Ford to bring the road to the vehicle, rather than the vehicle to the road.
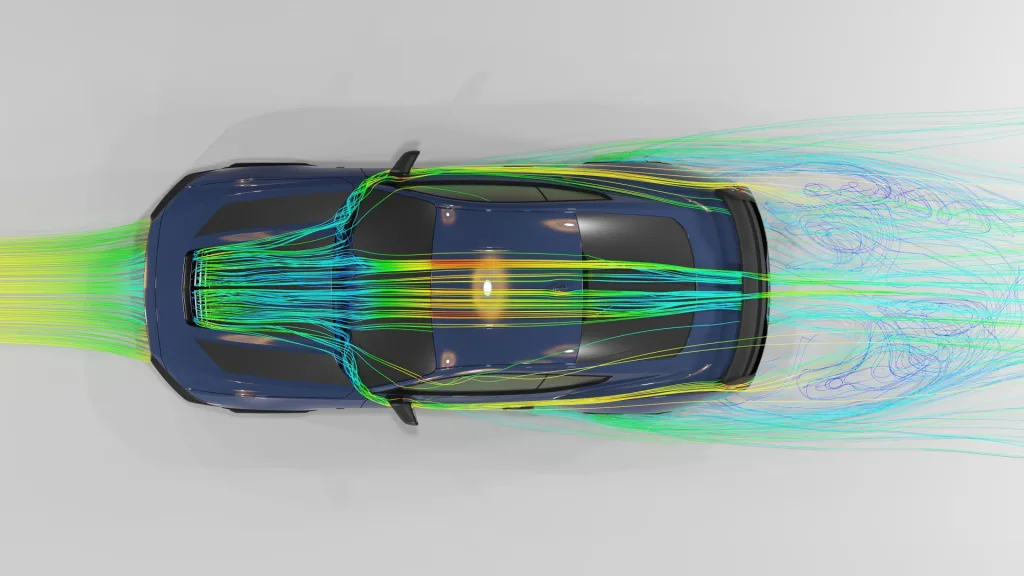
To test for optimal aerodynamic performance, each wheel gets its own belt, making up the first four belts. A large fifth belt runs under the centre of the vehicle. A crane is used to switch between the five-belt and single belt-systems – an industrial-sized plug-and-play. The single belt – which operates at up to 322km/h – opens up a new breed of testing for high-speed performance vehicles.
Maximising downforce on Mustang Dark Horse
The Mustang Dark Horse is among the first of many vehicles to be tested in this wind tunnel. Tailored aerodynamics are a key step in the development of new vehicles.
For passenger vehicles and trucks, the goal is to achieve low drag, creating a more efficient vehicle. However, for vehicles such as the Mustang Dark Horse that prioritise track-ready performance, aerodynamicists will trade low drag for increased downforce, which helps cars stick to the road or track and improves handling feel while cornering.
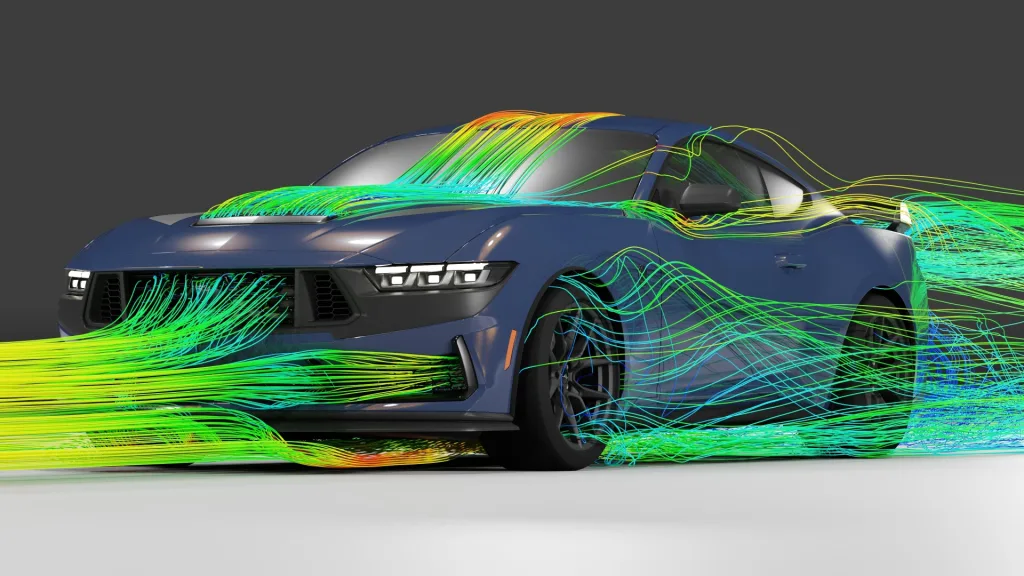
Overall, Mustang Dark Horse includes multiple changes and additional features, including a redesigned front bumper, a lower valence, a spoiler, and unique wheels. The front design is optimised to increase air flow for engine cooling, brakes and air intake, while also reducing front lift. On the Mustang Dark Horse, the lower air spoiler and splitter is unique, allowing the car to be tuned for greater downforce.
“We spent approximately 250 hours in the wind tunnel developing the 2024 Ford Mustang which includes Dark Horse,” said Program Aerodynamicist for Mustang and Bronco, Jonathan Gesek. “The aerodynamics of Mustang Dark Horse along with several other factors have created the most track- and street-capable 5.0-litre Mustang to date.”